Slitting and Rewinding 101: How Large Paper Rolls become Ready-to-Use Rolls and Sheets
May 22, 2025
Paper arrives from the mill in jumbo “parent” rolls – imagine an 8-foot-wide, one-ton spool of paper or linerboard. These giant rolls are too big for most printers or packaging machines. That’s where paper slitting and rewinding come in: specialized converting machines slice those parent rolls into narrower rolls that are easy to handle. In simple terms, a slitter rewinder unwinds a huge roll, cuts (slits) the web to the desired widths, then rewinds the strips onto new cores. This process is essential for converting large parent rolls of paper into more manageable sizes suitable for various applications.
Modern slitter-rewinders can handle a wide range of materials – not just paper. They process everything from kraft and linerboard (heavy packaging grades) to thin printing papers, even films and foils. For example, Cauthorne’s machines will happily slit thick brown kraft paper (used for bag-making or interleaving), sturdy linerboard, or lightweight coated print stock.
The key is versatility: by changing blades and settings, the same machine can tailor rolls of chipboard, tissue, waxed paper, and more. In fact, paper slitting machines are capable of processing various types of paper and flexible materials, including paperboard, film, foil, nonwovens, and laminates. This means whether you need narrow rolls of release liner for tape, long sheets of kraft for insulation, or standard print rolls, slitting/rewinding has you covered.
A slitter-rewinder machine processing a giant roll of paper. The unwound web will be cut by blades and rewound into smaller-diameter rolls.
The slitting & rewinding process works in three main steps:
- Unwinding: A giant parent roll is mounted on the machine’s unwind shaft. Heavy-duty arms or powered shafts support the roll. The web (paper) is pulled off the roll at speed.
- Slitting: As the web unwinds, it passes through a row of precise knives. These circular or razor blades slice the web along its length into narrower strips. For thin printing stocks, razor blades quickly and cleanly cut the paper. For heavier board or kraft, heavier-duty
shear blades (like scissors) may be used. (Shear slitting uses top-and-bottom circular knives and is ideal for very thick or tough materials.) The number of knives (and cut widths) is fully adjustable.
- Rewinding: After slitting, each cut strip of paper is immediately rewound onto a new core. Multiple rewind shafts (sometimes on a rotating turret) allow continuous operation: one roll winds while the next core is loaded. Tension controls and guide rollers keep the roll tight and even. When finished, you end up with many smaller rolls – each the exact width and diameter the customer needs.
Aside from slitting, these machines often include trim slitting and other finishing. Trim slitting cleans up the edges, and center perforation or embossing units can add features. Safety covers and sensors ensure operators stay protected. Today’s slitter-rewinders are often computerized, so an operator can dial in exact widths (even to 0.001″ tolerance), automatically align edges, and monitor tension.
The result of slitting and rewinding is a variety of customer-ready rolls. For example, a corrugated box maker might need 24-inch-wide rolls of linerboard from a 100-inch jumbo parent roll. The slitter-rewinder would slice that roll into four 24″ rolls (with a bit of trim) and rewind them to new cores. Each new roll can be any length or diameter; Cauthorne’s equipment lets us rewind to custom lengths or roll sizes. This
custom slitting is a key part of our paper cutting services – it saves customers the cost and hassle of buying oversized material and then cutting it themselves.
Machinery: Slitter Rewinders and Sheeters
These are the workhorses of roll conversion. A slitter rewinder looks like a row of shafts, rollers, and blade stations. In a two-shaft (turret) machine, one set of shafts unwinds a jumbo roll while two or more winding arms stand by. As each strip is cut, it automatically winds onto a fresh shaft.
Dual-drum or surface-winding configurations handle anything from tiny test rolls to massive production runs. For instance, duplex slitter rewinders can produce two smaller rolls at once.
Key features: adjustable tension control, computer knife positioning, and high-speed operation for maximum throughput.
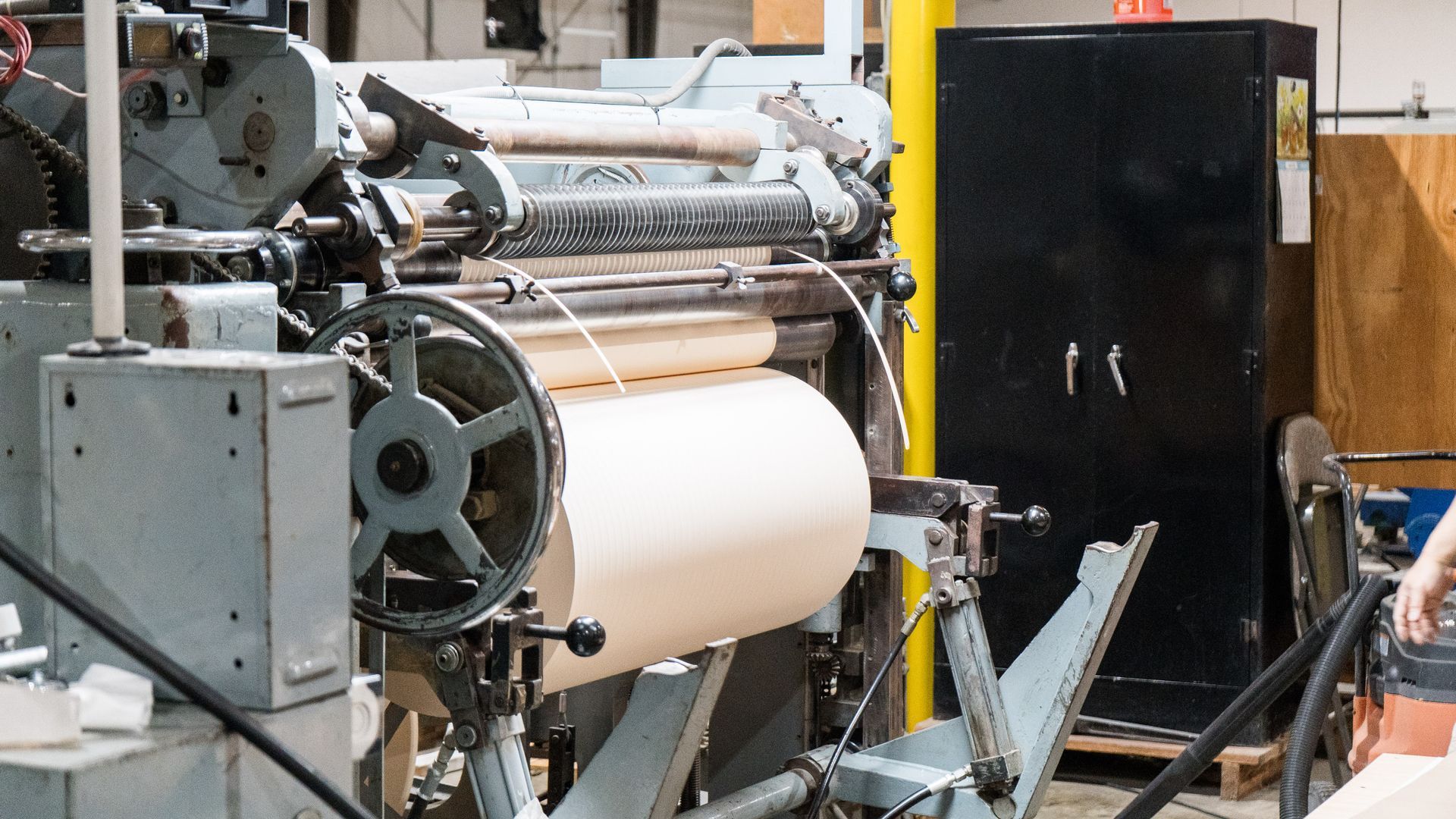
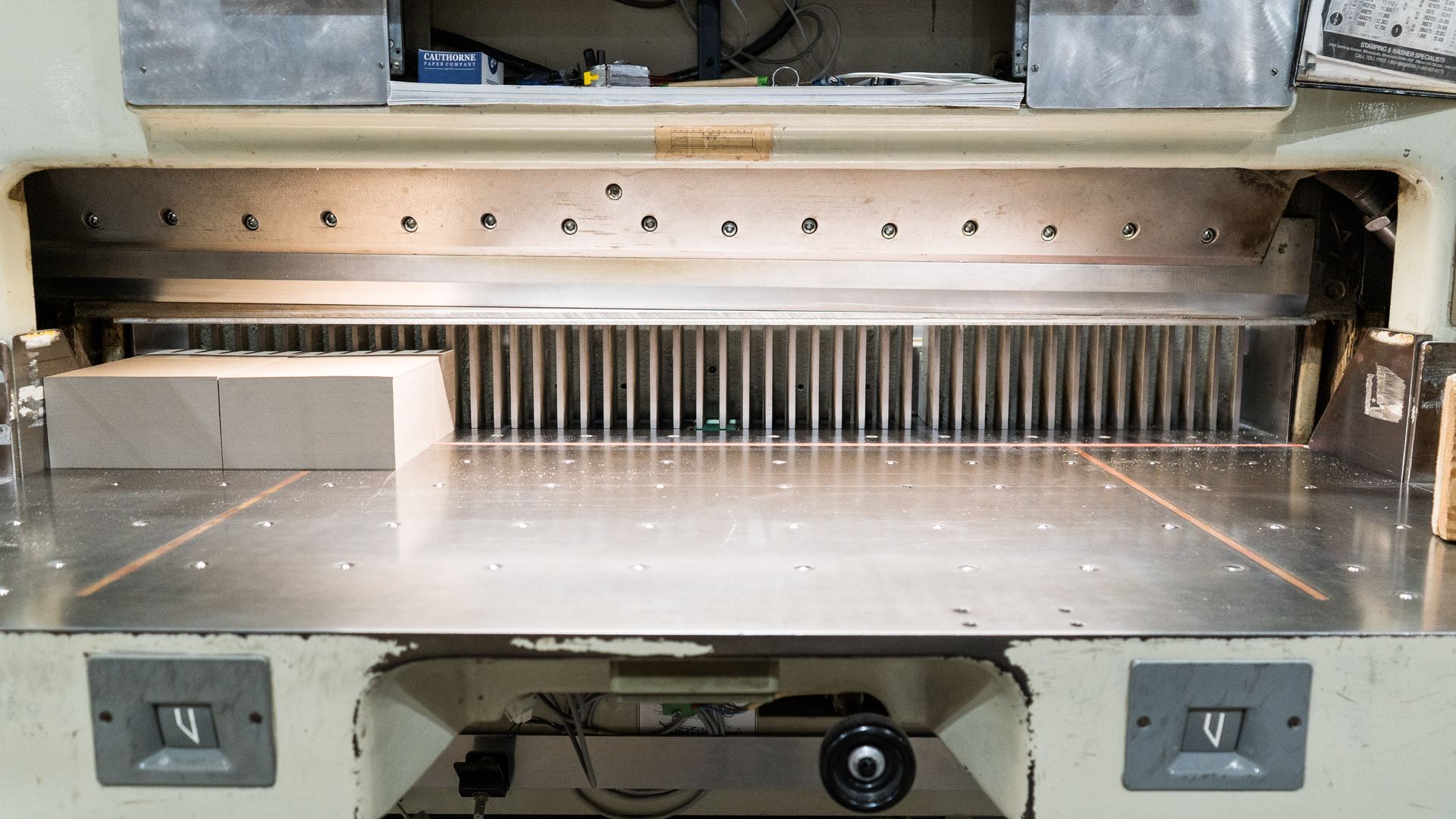
After slitting to width, many customers need flat sheets of paper. A sheeter is essentially a rolling web that feeds into a rotating knife. It converts a roll into stacks of sheets. As one example, our in-plant Sheeter can cut sheets up to 55″ long from the web.
The process is: unwind the slit roll, run it under a cutter, and cut at fixed intervals. If exceptionally short sheets are needed, we use high-precision guillotine trimmers. In short, sheeting and trimming are paper cutting services that turn rolls into ready-to-print or ready-to-convert sheets.
Whether using a slitter or a sheeter, our goal is always precision. As one manufacturer notes, the slitter-rewinder’s flexibility “allows for the customization of paper rolls to meet specific size and width requirements,” yielding custom-sized rolls for printing, packaging, and more. In practice, that means a roll of kraft can become many rolls of groceries bag stock, or a newspaper stock roll can become dozens of newsprint reels, all cut to spec.
Why Do We Slit and Rewind?
Slitting and rewinding solve real manufacturing puzzles. Here are some practical examples and benefits:
- Space & Shipping: It’s much more efficient to ship 30″-wide rolls than 150″-wide ones. Smaller rolls stack nicely on pallets and fit in customer machines. By slitting a parent roll into five smaller rolls, we reduce waste space and lower freight costs.
- Equipment Compatibility: A map-printing press might only take 40″ rolls, but the mill ships 80″ rolls. Slitting “bridges the gap,” quickly resizing the material. Similarly, a bag-making machine might need 36″ kraft rolls instead of the 96″ mill jumbo. Slitting rewinding provides exactly that.
- Quick Turnaround: Large distributors and converters rely on fast turnarounds. Using modern slitter rewinders, a one-ton roll can be processed in minutes. For example, one industry peer brought in a 10,000-pound linerboard roll on Monday, and by Tuesday had dozens of narrow rolls ready for their corrugator.
- Waste Reduction: Precision slitting minimizes scrap. If a customer needs an odd width (say 23.37″), we cut it exactly and can use trimmings for smaller orders or sample packs. In fact, custom slitting can cut waste (and cost) by getting the right sizes in one step.
- Versatility: One machine can handle kraft paper (brown, heavy-duty grades used for shopping bags and cartons), linerboard (paperboard used as corrugated facings), printing papers (newsprint, bond, coated, etc.), and more. We may use stiffer shear blades on heavy kraft/liner, or delicate razor blades for thin printing stocks. This versatility means our customers span many industries – from food packaging and industrial parts to publishing and textiles
Common Substrates
- Kraft Paper: A strong, often unbleached paper used in bags, wrapping, and interleaving. Its thickness can vary (30–80 lb base). Slitting kraft typically uses slower speeds and stout blades. Kraft rolls might be rewound coreless (wound on the paper itself) or onto cores.
- Linerboard: This is the flat paper used on top/bottom of corrugated board. It’s generally heavier (ranging up to 200 lb cover equivalent). Linerboard slitting is similar to cardboard sheeting – blades and pressure must handle its thickness without crushing.
- Printing Papers: Newsprint, book paper, coated stock, etc., are thinner (20–100 lb range) and often fragile. Razor slitting is ideal here, and tension control is critical. We can rewind large spools of coated stock (e.g. magazine grade) that go straight into presses.
- Tissue and Specialty Papers: While not all converting shops handle tissue, our slitter rewinders and sheeters can be set up (with webbing controls and perforators) to cut many types of tissue including napkin tissue and bath tissue.
Each material has its own rules, but the core idea is the same: start wide, end with customer-ready roll or sheet. Our team’s expertise (often guided by our in-house “Paper Doctor”) ensures the process is tuned for every substrate.
Slitting Methods
- Razor Slitting: Uses sharp razor blades mounted on holders. Excellent for thin, non-abrasive materials like paper or lightweight film. Quick changeover, good edge quality.
- Shear Slitting: Uses paired rotating circular knives (top/bottom like scissors). Ideal for heavy or abrasive materials (thick paperboard, metalized films, laminates). Produces very clean cuts on tough substrates.
- Score Slitting: One blade against a hard roll surface. Used for difficult-to-cut films or adhesive laminates. (Usually not needed for standard paper slitting – we primarily use razor or shear.)
Each slitter-rewinder machine may be set up differently: some have fixed knives (steel rules), others have pneumatic or manual adjustment for quick blade changes.
Example: Converting a Jumbo Roll
Let’s walk through a quick example. Suppose a manufacturer receives a 91-inch-wide roll of kraft paper from the mill, weighing 3,000 pounds. They need 12″-wide rolls to feed into their bag machine, and about 500 feet long each. Here’s what happens:
- Receive & Mount: The operator places the jumbo roll on the slitter machine. Safety checks are done.
- Setup: The operator (or our technician) programs the slitter to cut 12″ widths and calibrates tension. Razor knives are positioned every 12″.
- Process: The roll unwinds, and the knives slice the web into about 7 strips (since 91″ / 12″ ≈ 7.5, so we trim off the extra). Each strip winds onto a new core simultaneously.
- Output: Within minutes, seven small rolls (12″ × 500′ each) come off the machine, plus a trim roll (which we save or recycle). The customer’s required roll size is now complete.
Later, if the customer also needs 24″×36″ sheets of that same kraft, we could use a similar roll and slit to 24 and take those ″ rolls to a sheeter. The sheeter would cut sheets to 36″ length, stacking them for delivery or further die-cutting.
Integration into Paper Cutting Services
At Cauthorne Paper, slitting and rewinding is part of our broader paper cutting services menu. We don’t just slit – we can also slit-to-width, sheet-to-length, and die-cut if needed. Many customers call us for “paper cutting services” when they need non-standard sizes or quick turnarounds. For example:
- Packaging industry: needs custom wrap sheets or roll lamination stock. We slit 80″ rolls into 20″ rolls and sheet it for die-cutting.
- Printer: orders 48″ rolls of glossy paper for a run, not wanting to buy an 80″ roll. We slit their glossy roll to 48″ and rewind.
- Nonwoven/textile: even fiber manufacturers have used our services to convert specialty fibers on paper rolls.
We often describe our work as solving paper puzzles. Whether it’s producing the exact roll diameter a customer specified, or handling a delicate thermal paper stock without tearing, we adjust our process. In fact, Cauthorne’s slitting/rewinding services “are customized to the specific needs of our customers. We can slit a variety of materials to custom widths and rewind to custom lengths or roll sizes”– exactly the kind of flexibility today’s converters demand.
Getting Started
If your manufacturing or converting operation has unusual paper needs, we’re here to help. Have a roll that needs resizing, a new sheet size, or a tricky substrate? Reach out!
Cauthorne Paper’s team (including our friendly “Paper Doctor” Steve Newsome) would be happy to discuss how slitting, rewinding, and sheeting can work for you. Whether you simply have a question about paper slitting or you’re ready to arrange a quote for paper cutting services, we can assist. Let us be the solution to your paper processing needs – our century-plus of experience means we speak your (paper) language.
Ready to work with Cauthorne Paper?
Let's connect! We’re here to help.
Send us a message and we’ll be in touch.
Or give us a call today at 804-798-6999
Agency Contact Form
More on Paper
The Rollout

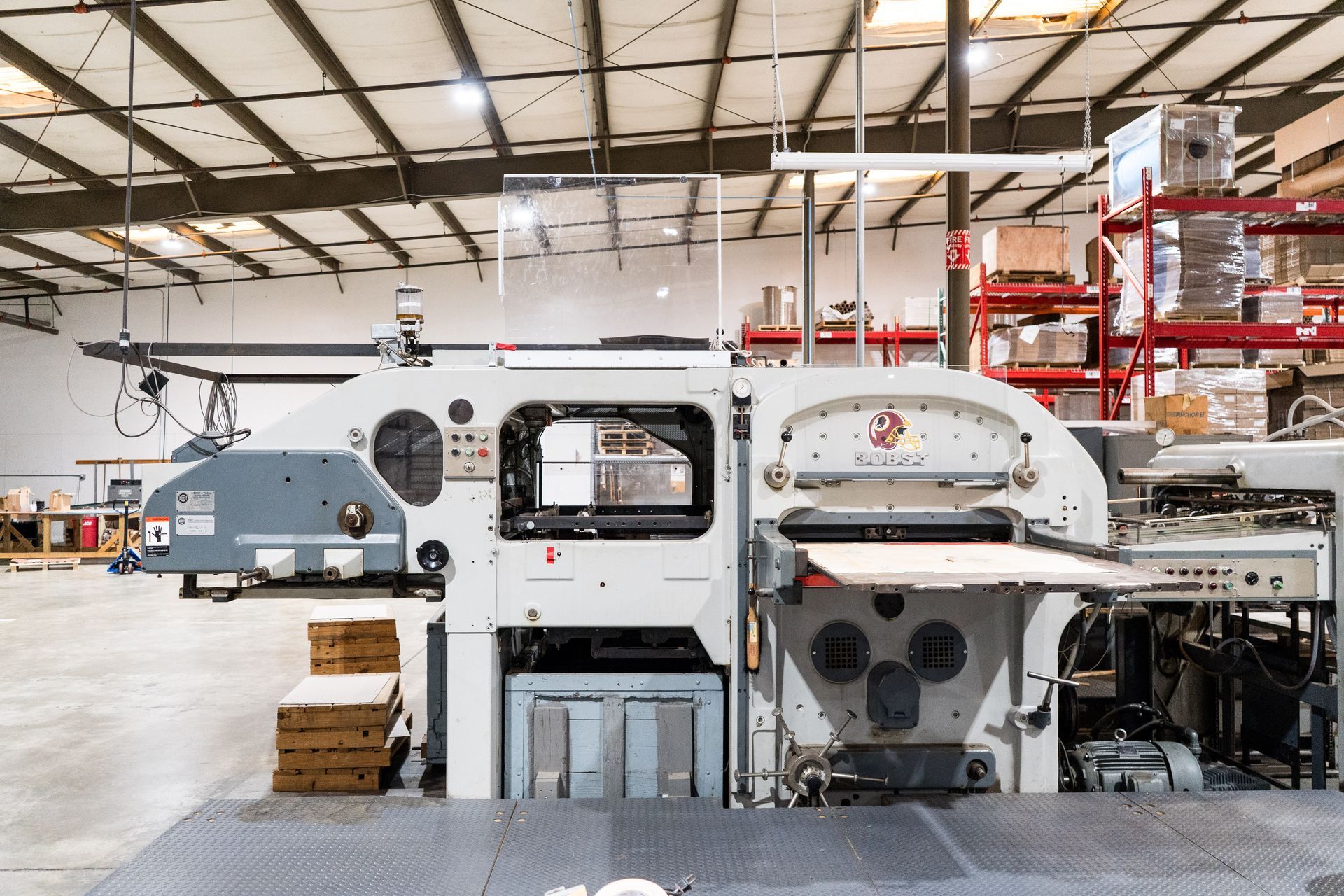
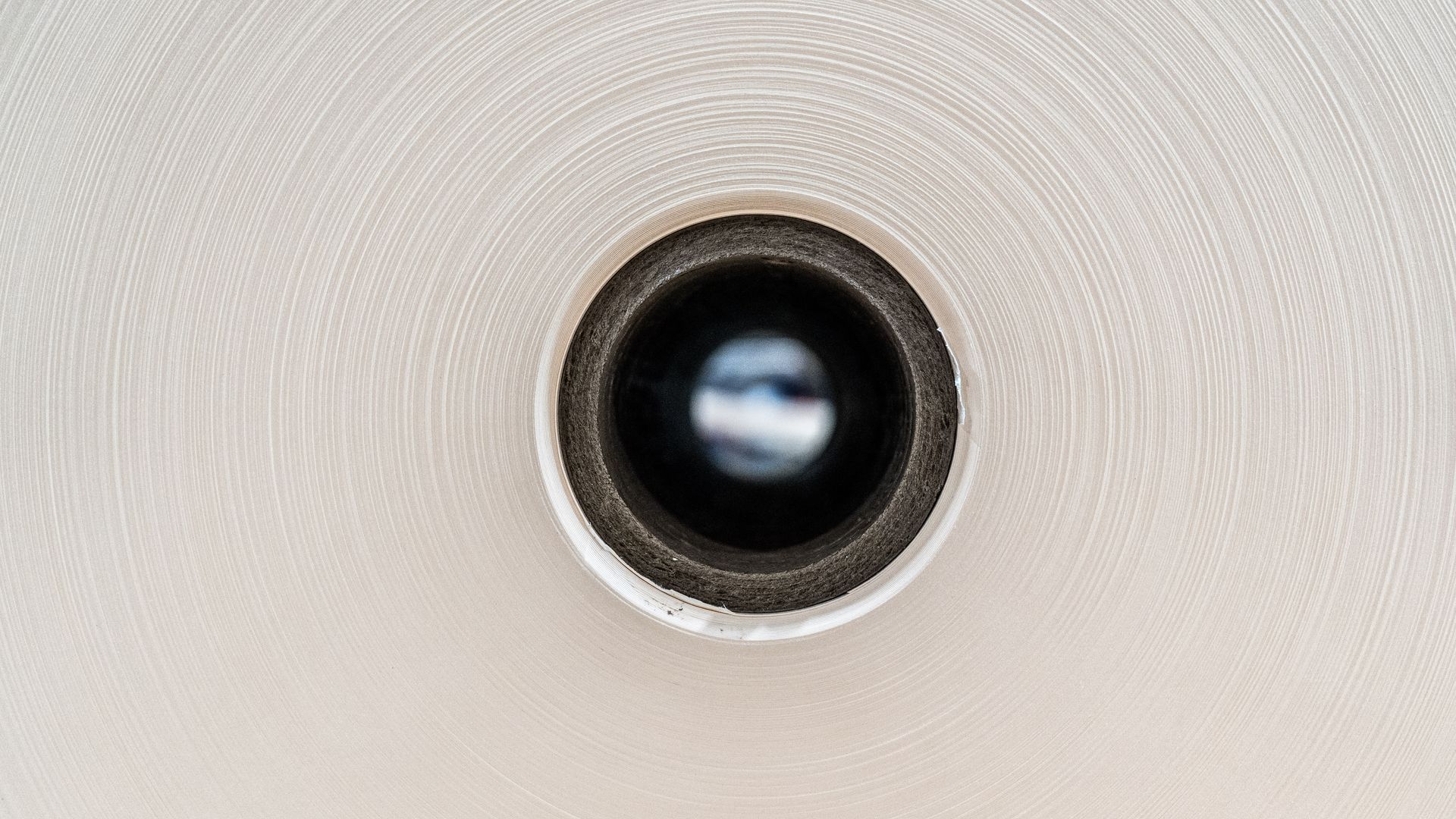