What Is Custom Paper Converting? Tailoring Solutions to Unique Packaging Needs
May 28, 2025
Custom paper converting is the process of taking raw paper materials (usually large “parent” rolls or sheets) and transforming them into precisely the sizes and formats a customer needs. In practice, converting means cutting, trimming, rewinding, and otherwise modifying paper so it’s ready for use in packaging or manufacturing. Rather than selling standard roll or sheet sizes, a custom converting partner customizes the material. For example, a converter can slit a jumbo roll of kraft paper into narrower rolls or sheet it into panels sized for your machine. In short, converting turns generic paper products into tailor-made solutions for downstream processes.
Converting Services: Slitting, Sheeting, Trimming, Labeling, and More
Custom converters offer a range of specialized services to meet unique packaging needs. Precision equipment is used at every step – from slitters to sheeters to guillotine cutters. For instance, converters use guillotine-style trimmers(as shown below) to trim stacks of paper with clean, square edges. These machines and others ensure each cut is accurate and efficient.
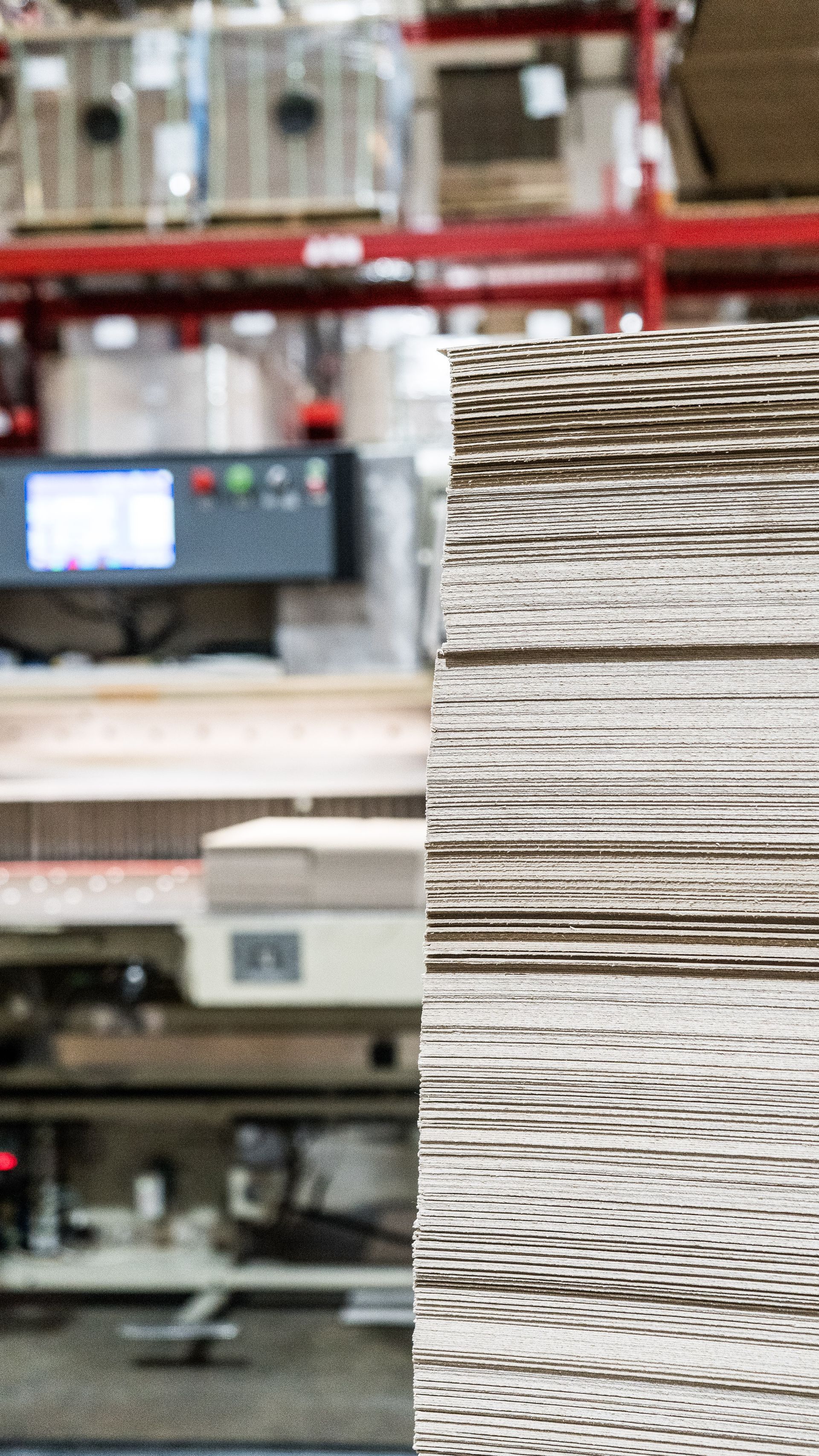
Cutting wide paper rolls into narrower rolls of specified width. Slitting tailors the material to fit specific machinery or packaging requirements. Large “master” rolls (for example, 80″+ wide) can be cut down to any needed width. This reduces roll weight and waste, making the material ready for your equipment. (As one converter explains, slitting “prepares raw materials for your machines,” matching roll widths to production needs.)
Cutting rolls into individual sheets of a precise length. A sheeter pulls paper off the roll and slices it into flat sheets at exactly the requested dimensions. This is crucial when downstream processes (like printing, lamination, or folder-gluer operations) require specific sheet sizes. Sheeting ensures uniform, stackable sheets – for example, cutting a roll into 28″×44″ sheets for the printing industry.
Using a heavy-duty blade to trim stacks of sheets to finished size. After sheeting, converters often use a hydraulic guillotine cutter to make very clean, square cuts. Guillotine trimming is also ideal for jobs the main sheeter can’t handle (such as extra-short runs or boards thicker than the sheeter’s capacity). This yields paper or board stacks with perfect edges. Some converters even bundle the trimmed sheets in uniform packets for easy handling.
Applying identification labels to rolls or bundles for traceability. Converters can print or apply labels that include information like product name, roll length, batch number, and order details. Clear roll labeling prevents mix-ups on the production line. For example, one converter notes that all slit rolls are labeled with product name, length of roll, PO #, Roll ID #, date of manufacturing. This means when your operators load a roll, they immediately know exactly what it is and how to use it.
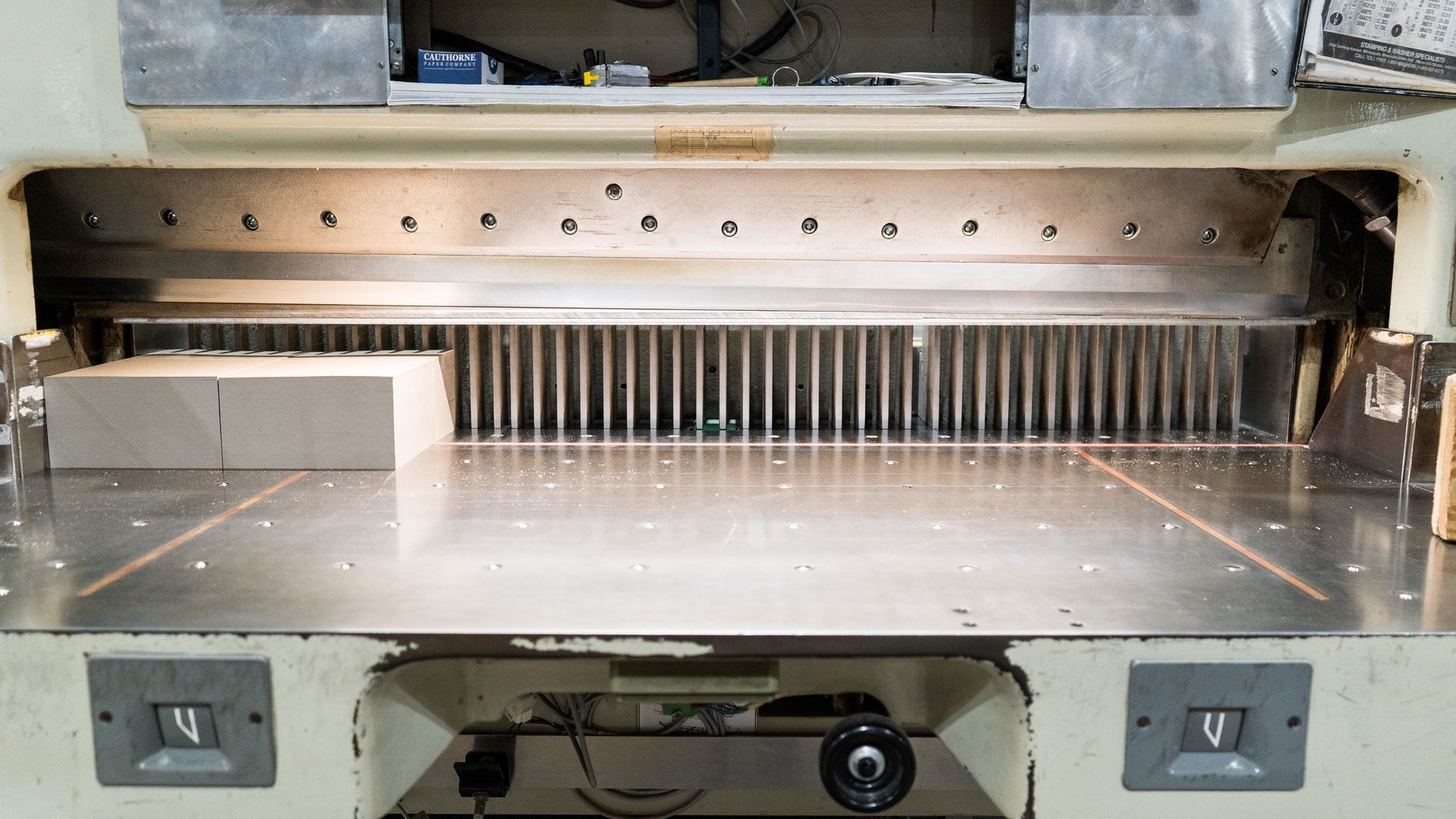
Each service is adaptable. A good converter will work with your specs – handling everything from very large runs to one-off prototypes – and combine these services as needed to create the right finished product.
Materials Commonly Converted
Converters work with a wide variety of paper and board materials. Our common substrates include:
- Kraft Paper (natural or bleached): Strong, uncoated papers used for bags, envelopes, tape backings, and corrugated facings. Kraft is a workhorse material for packaging and industrial uses.
- Newsprint and Bond Papers:
Lightweight, general-purpose stocks (often recycled) for everything from interleaving to printing.
- Linerboard and Chipboard: Heavier paperboards used in box making. Linerboard is the flat paperboard for corrugating; chipboard (also called binder’s board) is rigid board used in shoe boxes, appliance backs, or other industrial packaging. Converters can slit and sheet these thick boards for your needs.
- Waxed and Poly-Coated Papers: Papers treated with wax or plastic coatings for moisture, grease or chemical resistance (think oil-barrier bagging paper, for example). Converting can slit or sheet these specialty papers just like regular paper.
- Release Liners: Silicone-coated paper used as backing for adhesive labels and tapes. Converters often slit release liner rolls or make smaller sheets to feed label presses. In fact, one converter explicitly lists “release liner” among the substrates it handles.
- Coated and Specialty Stocks: Any
sort of coated papers or boards (like
SBS
C1S/C2S
clay-coated board, CUK board, glossy or matte paper, etc.). These are common for graphics and packaging, and converting partners have equipment to cut and rewind them without damaging the coating.
In addition to the above, converters can often work with synthetic or composite materials (foils, laminates) and non-wovens if needed. The key is that they match their equipment and processes to your material.
Solving Real Packaging Challenges
Custom converting shines when off-the-shelf sizes just won’t work. Some illustrative examples:
- Scaling Down Jumbo Rolls: A paper mill might supply a single 100″ wide roll, but your press or laminator only accepts 50″ rolls. A converter will slit that giant roll into two 50″ rolls (or more if needed). This maximizes yield and eliminates excess trim waste. For instance, converting can turn an 88″ kraft roll into 4 narrower 22″ rolls (with minimal leftover trim) so each fits standard equipment. Converters routinely handle “mega-rolls” and reduce them to “usable-size rolls” for packaging customers.
- Custom Sheet Sizes: Suppose you need sheets of 48″×96″ for a die cutter, but standard off-the-shelf is 40″×60″. A converting partner can run the paper through a wide sheeter and a guillotine to produce your exact panel size. This avoids having to trim sheets by hand or waste excess. Custom sheeting is invaluable for unusual dimensions, specialty cartons, or when tight tolerances are required.
- Detailed Labeling for Production: In fast-moving lines (like film coating or printing), knowing exactly which roll or sheet is loaded saves time. Converters can apply durable labels to each roll or bundle. For example, one converter’s practice is: “All slit rolls are labeled with product name, length of roll, PO #, Roll ID #, date of manufacturing”. That means every roll arriving at your dock comes clearly marked, eliminating guesswork for machine operators.
- Tailored Bundling & Packaging: Consider a situation where 500 sheets of coated board need to be shipped safely. The converter can bundle them in layers with slip sheets, band them, and wrap the stack in plastic film according to your spec. For rolls, converters will build pallets “to customer and product specification with no material overhang,” applying strapping and shrink-wrap as needed. This customized pack-out ensures the material arrives undamaged and ready to use.
In each case, the converter works closely with the customer to understand the downstream process. Whether it’s adjusting roll widths, changing sheet formats, or adding scannable labels, custom converting solves problems that off-the-shelf products can’t.
Benefits of an Experienced Converting Partner
Working with a seasoned converter brings important advantages:
- Industry Expertise. A converter with decades of experience has deep know-how. For example, Cauthorne Paper emphasizes that with “over a century in the paper converting business, we bring unmatched knowledge and craftsmanship to every project”cauthornepaper.com. This means fewer surprises on specs or material behavior. Veteran converters understand which paper stocks convert cleanly, how moisture content affects cuts, and what packaging each type needs.
- Flexibility & Capacity. A good partner can handle everything from large production runs to one-time custom jobs. Cauthorne notes that “from large-scale runs to custom orders, our team adapts to meet your unique needs with precision and efficiency”. So whether you need 100 rolls on short notice or a precise batch of prototype sheets, a flexible converter will adjust machinery and schedules to deliver on time.
- Inventory and Turnaround. Leading converters often maintain substantial inventories of popular papers and convert them quickly. This means you avoid weeks of wait time – the converter can ship standard materials from stock or run custom converting quickly rather than ordering new parent rolls.
- Value-Added Service. Beyond cutting paper, a top converter is a problem-solving partner. As Cauthorne’s site states, their goal is to be a “value-added supplier” that even assists with R&D projects and sourcing raw materials. In practice, this might mean the converter helps you test a new paperboard grade, recommends a more cost-effective stock, or tweaks machine settings. They serve as consultants, leveraging their conversion expertise to improve your product and process.
- Strong Supply Relationships. An established converter has long-standing relationships with paper mills. This often translates to better material availability and competitive pricing. It also means the converter knows alternative sources if a particular paper grade is back-ordered, helping prevent production delays.
In short, an experienced converting partner combines technical skill, flexible production, and customer service. This results in higher-quality output, more reliable delivery, and often lower total cost of ownership – you’re buying exactly what you need, with minimal waste or downtime.
Getting Started: Consult with the Experts
If your operation is struggling with unusual paper sizes or packaging requirements, it’s worth reaching out to a custom converter. Start by describing your needs – the paper grade, original roll size, and the final form or packaging you require. Many converters (like Cauthorne) offer consultative quoting: they’ll advise on the best converting approach. Often a quick call or form submission can yield a plan or sample to test.
Think of a custom converter as part of your supply chain engineering: they can make your process smoother by delivering ready-to-use paper. So, for oversized rolls, odd dimensions, special coatings, or any tricky request, don’t hesitate to ask. A knowledgeable converter will collaborate with you to tailor a solution, whether that means slitting to exact widths, adding precise labels, or packaging the bundles for your line.
Ready to solve your paper packaging puzzle?
Contact a reliable converting partner today. They can work through your specs and provide a quote – and often the initial consultation is free. By partnering with a flexible, experienced converter, you’ll get the exact paper rolls, sheets, labels, and packaging you need to keep your production running smoothly.
Ready to work with Cauthorne Paper?
Let's connect! We’re here to help.
Send us a message and we’ll be in touch.
Or give us a call today at 804-798-6999
Agency Contact Form
More on Paper
The Rollout

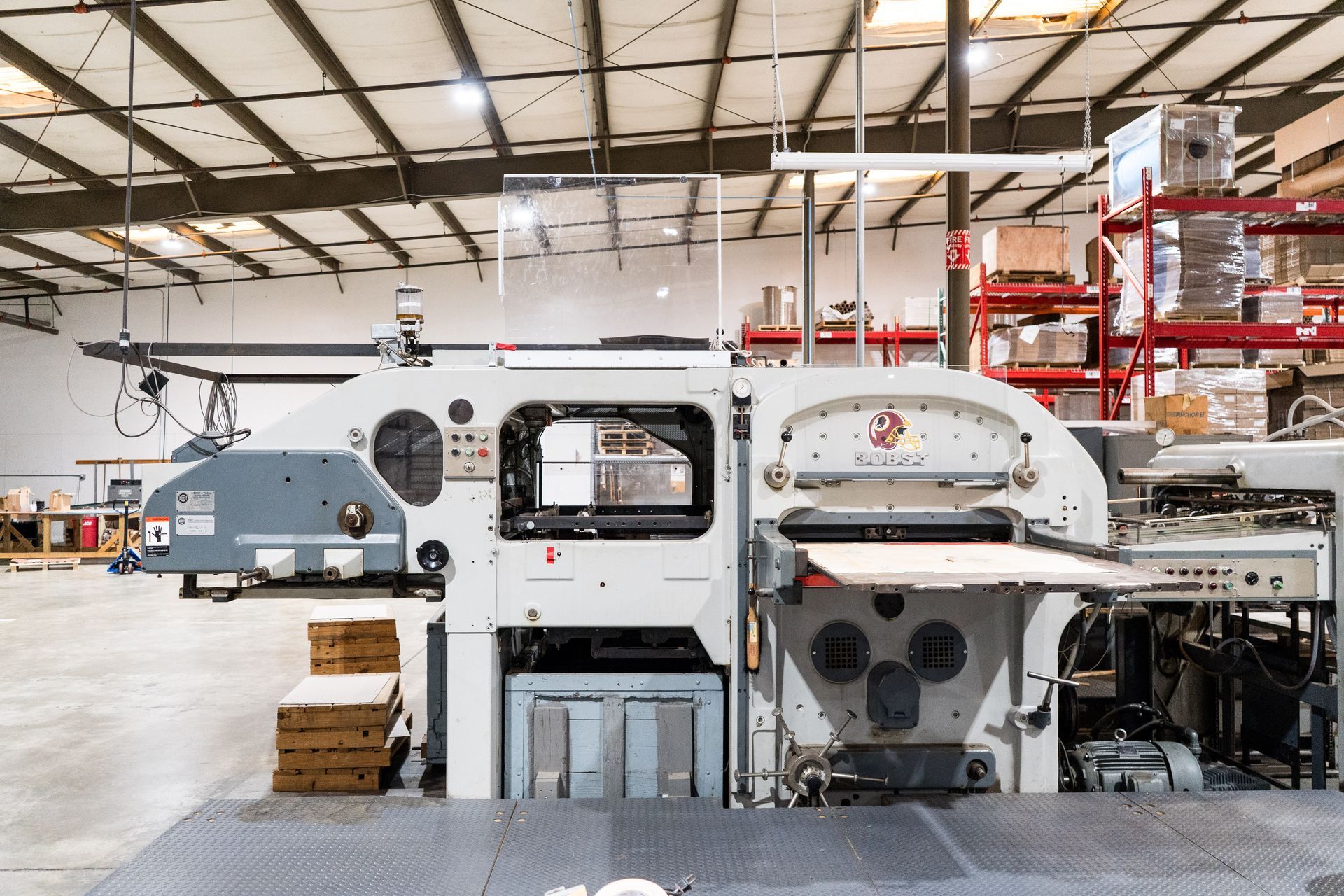
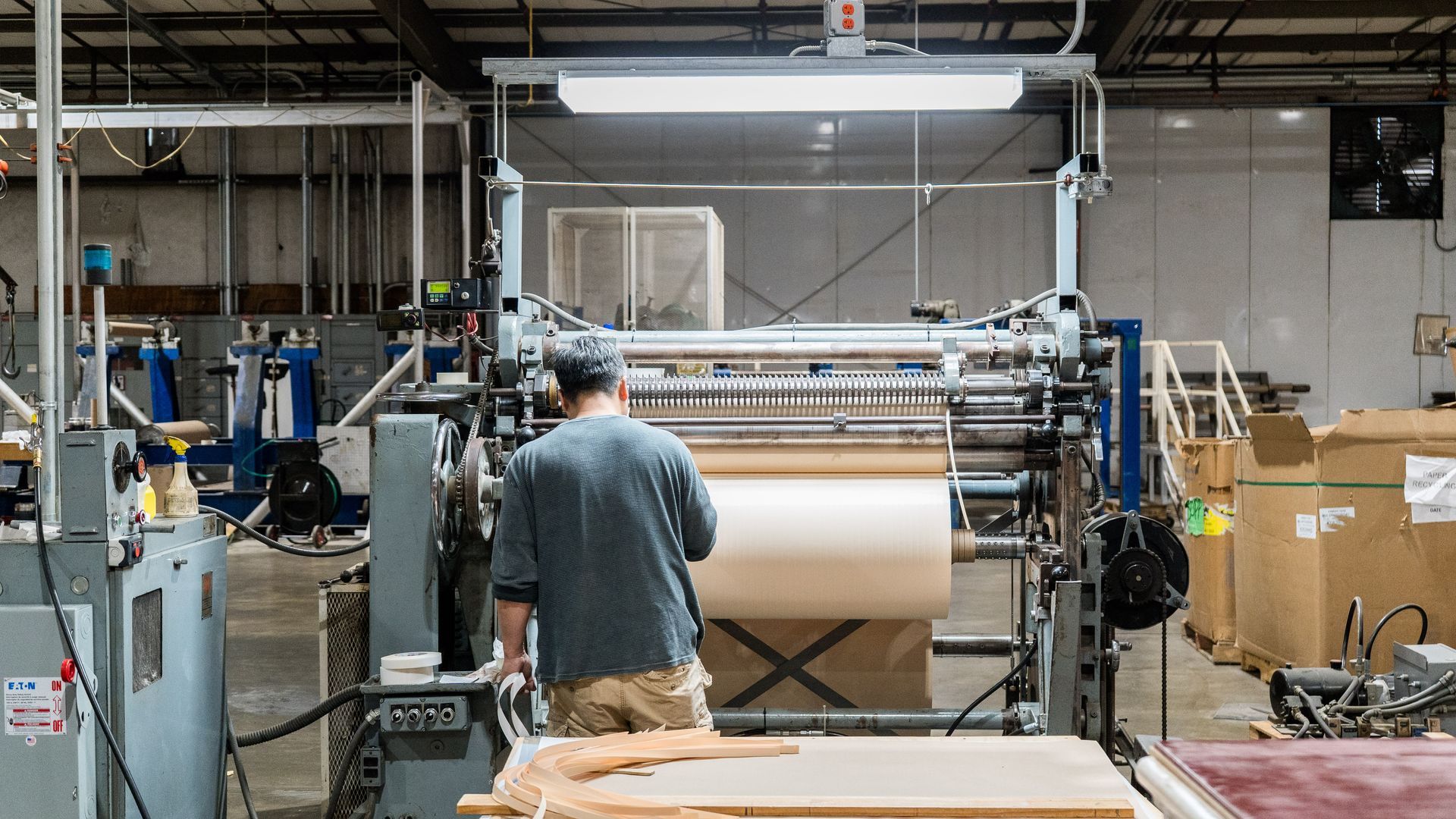