The Rollout
The Rollout is your go-to source for industry trends, converting tips, sustainability updates, and everything happening behind the scenes in the world of paper. From innovations in slitting and sheeting to supply chain insights, we unpack it all—one layer at a time.

When it comes to custom paperboard converting, attention to detail can make the difference between a smooth production process and costly delays. Mistakes in your order can result in wasted materials, misfit products, and frustration for your team. Whether you’re using slitting and rewinding, sheeting and trimming, or die cutting, knowing the most common pitfalls can help you make the most of your paperboard converting services.
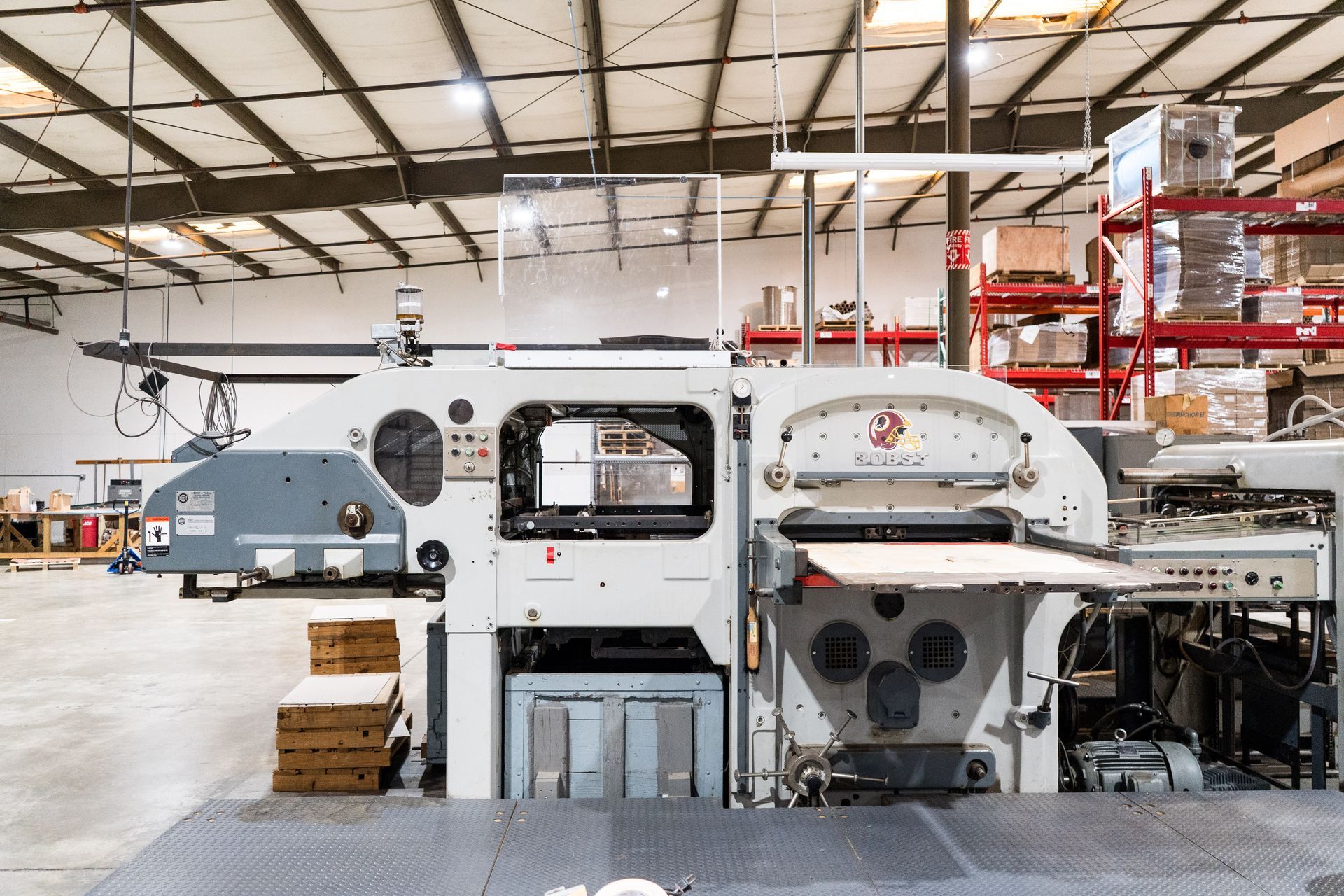
At Cauthorne Paper , quality is the foundation of everything we do. For over a century, our team has specialized in paper slitting and rewinding, sheeting, trimming, die cutting, and more, delivering “precision and versatility with every cut”. We bring that same commitment to every order, whether it’s a large-volume roll or a detailed custom design. Manufacturers and businesses can rely on our paper converting services knowing we follow proven processes, strict inspections, and continual improvement at every step. In short, we treat your project as our own – ensuring the final product meets your exact specifications and our high quality standards. Advanced Converting Services with Built‑In Quality Cauthorne Paper offers a full range of custom converting services, from paper slitting and rewinding to die cutting, sheeting, and packaging. Across all these services, we use state-of-the-art equipment and precise methods to ensure consistent results. For example, our slitting machines use precision shear knives that deliver a “superior cut with a precision edge” This means every slit roll comes off the line with clean, square edges and exact dimensions. We can slit rolls to virtually any width (from 3/8″ up to 70″) and rewind them to customer-specified lengths and core sizes, always meeting your tolerance requirements. Paper Slitting & Rewinding: Our customized slitting process lets us cut large master rolls into narrow or wide rolls with tight dimensional accuracy. We tailor each slitting setup to the material and specs at hand. An advanced inventory control system tracks every roll from receipt to finished product, so raw materials and finished rolls are “easily identified and monitored at every stage of the process”. We can apply barcode labels or custom tags to each roll so it’s traceable through your supply chain. Sheeting & Trimming: Once rolls are slit, our sheeter and guillotine trim equipment cut sheets to precise lengths and sizes. For example, our guillotine trimmers can cut sheets as small as 1″×1″ with exceptionally tight tolerances. In fact, our guillotine can hold tolerances down to 1/32″. This level of precision lets us meet even the most exacting length and size requirements. After cutting, we offer custom finishing options – from ream wrapping and boxing to palletizing – to ensure each stack of sheets is packaged neatly for shipping. Die Cutting: Our die cutting capabilities let us create virtually any shape from chipboard, folding carton, or corrugated material. We use CAD design and a Gerber sample table to prototype and fine-tune designs, then run them on our high-tonnage die cutter. The machine is optimized for quality: it offers a max tonnage of 550 tons and “excellent print to cut registration and stripping capabilities”. In practice this means printed designs align perfectly with the cut outlines. Whether it’s standard packing inserts or intricate shapes for specialty packaging, our die cutter delivers consistent, clean cuts run after run. Our modern converting machinery, like this calibrated high-speed press, is kept in peak condition to guarantee precise output. Every cutter, slitter and shear knife is regularly maintained and calibrated so dimensions and registration stay on spec. When a project calls for fine tolerances (for instance, cutting decorative labels or precision gaskets), our calibrated equipment and experienced operators hit the mark every time. Meticulous Quality Control & Traceability Quality isn’t an afterthought – it’s built into our process from start to finish. Each job begins with a detailed review of customer specifications, samples, and any special requirements. We inspect incoming paper or board materials before they enter production, checking weight, grade and condition. Throughout production, operators follow standardized work instructions and record key measurements. At critical points we perform in-process inspections: for example, after slitting, we verify roll widths and edge quality; after cutting, we check sheet dimensions and stack counts. Finally, finished products undergo a last quality check against the original specs. Key parts of our quality system include: Systematic Inspections: Every batch is logged with a job number, and our team conducts incoming inspections on raw rolls (confirming the material grade and dimensions) and outgoing inspections on finished goods. Checklists are used at each stage to ensure nothing is overlooked. Our operators have earned praise for their diligence – as one manager noted, the team consistently meets customer requirements “efficiently and with minimal waste”. Documentation & Tracking: We use digital job-tracking software (PaperSoft) to document each step of production. This means every order has a paper trail, from the original purchase order and material certificates to machine settings and inspection results. We label finished rolls and sheet bundles with identifying barcodes and packing lists, so the origin and details of every item can be traced instantly. This chain-of-custody approach is especially important for customers requiring certified or recycled materials. Equipment Calibration: All cutting, measuring and testing equipment is on a strict calibration schedule. For example, our measuring gauges and width sensors are checked against standards to maintain their accuracy. This complies with ISO 9001 practices and ensures that what our machines tell us matches reality. If an instrument or blade drifts out of spec, we recalibrate or replace it immediately. This way, every operation, slitting, sheeting or die cutting, stays true to the tolerances we promise. Continuous Improvement (5S, Lean): We maintain a lean, organized shop floor. Workstations are arranged for efficiency (5S principles), tools are labeled and easy to find, and any process changes are documented as new standard work. This consistent organization reduces errors and variability. In fact, we’ve brought outside experts in-house to help refine our processes – like our Lean Six Sigma Black Belt, Tom Zbell, implementing things like work-center instructions and set-up reduction because as one industry advisor put it, these successes “show that Mark is serious about providing a top quality product to his customers through continuous improvement”cauthornepaper.com. By combining these controls with our skilled, long-tenured workforce, we deliver remarkably consistent results. We treat each converted roll and die-cut blank as if it were destined for our own product , the same high standards apply. Ready to experience a quality-focused converting solution? Contact our team today and let’s discuss your project. Whether you need small custom runs or large production jobs, we’re here to roll up our sleeves and make it happen with precision and care. Reach out for a quote and let us put our quality assurance to work for you!
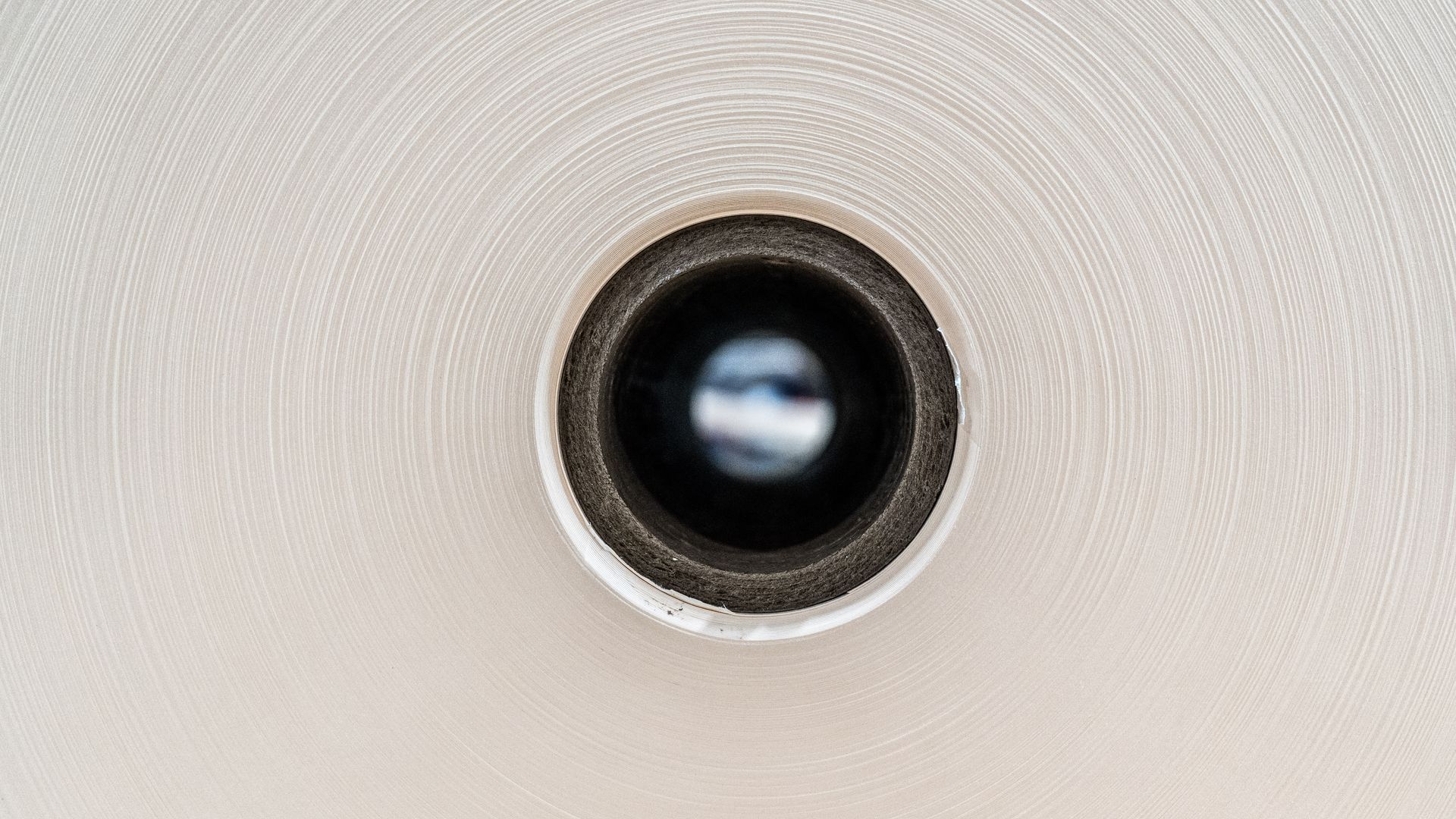
Custom paper converting is the process of taking raw paper materials (usually large “parent” rolls or sheets) and transforming them into precisely the sizes and formats a customer needs. In practice, converting means cutting, trimming, rewinding, and otherwise modifying paper so it’s ready for use in packaging or manufacturing. Rather than selling standard roll or sheet sizes, a custom converting partner customizes the material. For example, a converter can slit a jumbo roll of kraft paper into narrower rolls or sheet it into panels sized for your machine. In short, converting turns generic paper products into tailor-made solutions for downstream processes.
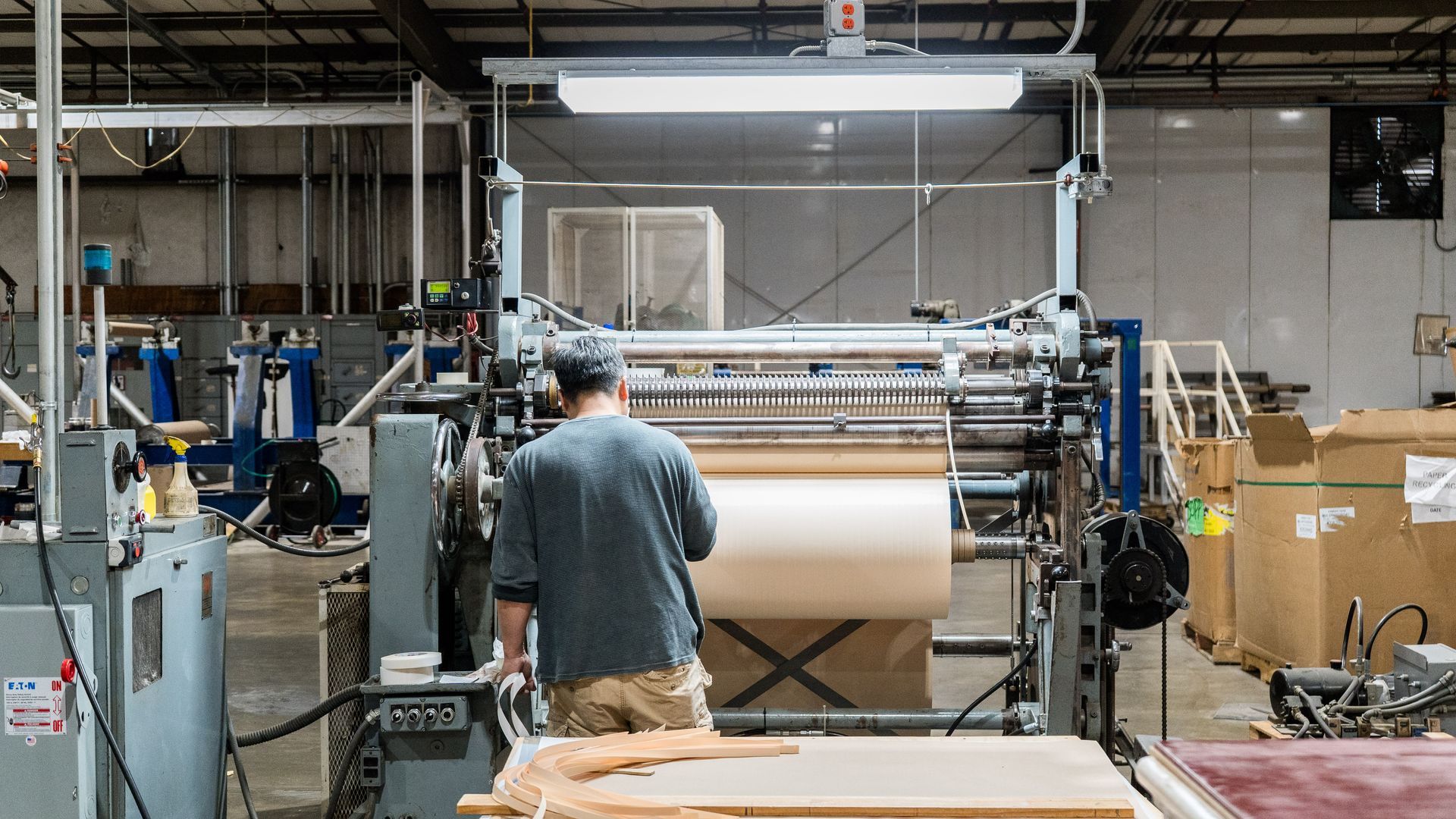
Paper arrives from the mill in jumbo “parent” rolls – imagine an 8-foot-wide, one-ton spool of paper or linerboard. These giant rolls are too big for most printers or packaging machines. That’s where paper slitting and rewinding come in: specialized converting machines slice those parent rolls into narrower rolls that are easy to handle. In simple terms, a slitter rewinder unwinds a huge roll, cuts (slits) the web to the desired widths, then rewinds the strips onto new cores. This process is essential for converting large parent rolls of paper into more manageable sizes suitable for various applications. Modern slitter-rewinders can handle a wide range of materials – not just paper. They process everything from kraft and linerboard (heavy packaging grades) to thin printing papers , even films and foils. For example, Cauthorne’s machines will happily slit thick brown kraft paper (used for bag-making or interleaving), sturdy linerboard, or lightweight coated print stock. The key is versatility : by changing blades and settings, the same machine can tailor rolls of chipboard, tissue, waxed paper, and more. In fact, paper slitting machines are capable of processing various types of paper and flexible materials, including paperboard, film, foil, nonwovens, and laminates. This means whether you need narrow rolls of release liner for tape, long sheets of kraft for insulation, or standard print rolls, slitting/rewinding has you covered. A slitter-rewinder machine processing a giant roll of paper. The unwound web will be cut by blades and rewound into smaller-diameter rolls. The slitting & rewinding process works in three main steps: Unwinding: A giant parent roll is mounted on the machine’s unwind shaft. Heavy-duty arms or powered shafts support the roll. The web (paper) is pulled off the roll at speed. Slitting: As the web unwinds, it passes through a row of precise knives. These circular or razor blades slice the web along its length into narrower strips. For thin printing stocks, razor blades quickly and cleanly cut the paper. For heavier board or kraft, heavier-duty shear blades (like scissors) may be used. (Shear slitting uses top-and-bottom circular knives and is ideal for very thick or tough materials.) The number of knives (and cut widths) is fully adjustable. Rewinding: After slitting, each cut strip of paper is immediately rewound onto a new core. Multiple rewind shafts (sometimes on a rotating turret) allow continuous operation: one roll winds while the next core is loaded. Tension controls and guide rollers keep the roll tight and even. When finished, you end up with many smaller rolls – each the exact width and diameter the customer needs. Aside from slitting, these machines often include trim slitting and other finishing. Trim slitting cleans up the edges, and center perforation or embossing units can add features. Safety covers and sensors ensure operators stay protected. Today’s slitter-rewinders are often computerized, so an operator can dial in exact widths (even to 0.001″ tolerance), automatically align edges, and monitor tension. The result of slitting and rewinding is a variety of customer-ready rolls. For example, a corrugated box maker might need 24-inch-wide rolls of linerboard from a 100-inch jumbo parent roll. The slitter-rewinder would slice that roll into four 24″ rolls (with a bit of trim) and rewind them to new cores. Each new roll can be any length or diameter; Cauthorne’s equipment lets us rewind to custom lengths or roll sizes. This custom slitting is a key part of our paper cutting services – it saves customers the cost and hassle of buying oversized material and then cutting it themselves.